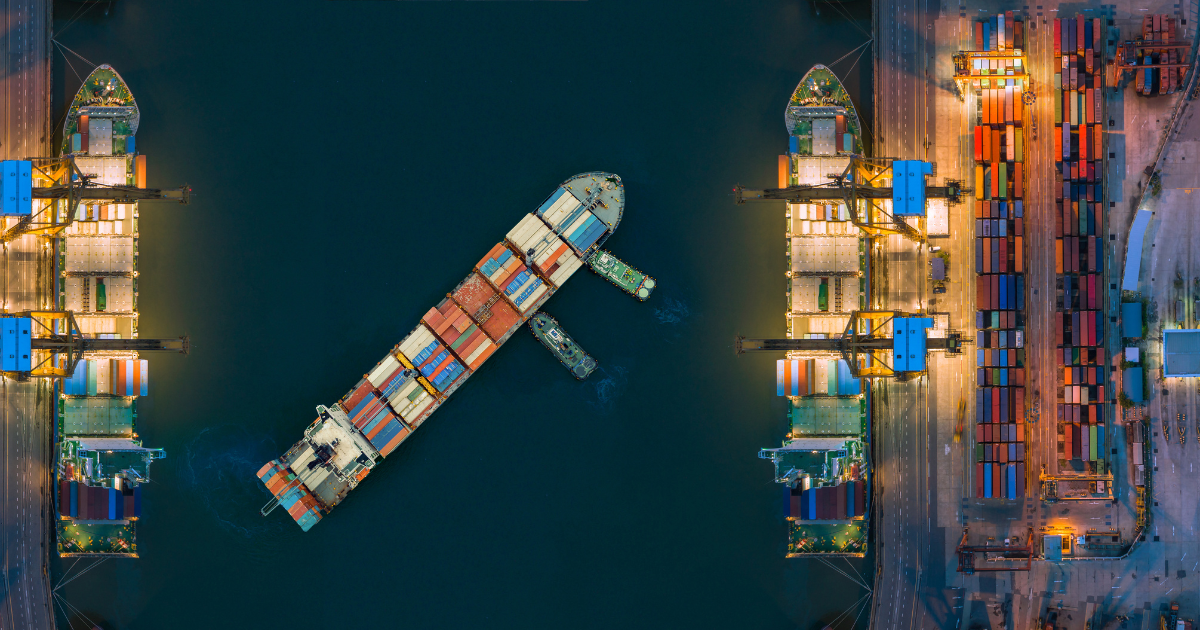
How to make logistics adaptive and prepare for uncertainty
By Thilina Siriwardena, Chief Executive Officer
Disruptions and uncertainty have always existed globally. The recent global pandemic, however, turned things upside down for many industries. For the logistics industry, the pandemic strained supply chains to their breaking point and sent businesses scrambling to adjust to a new reality.
Having a resilient and adaptable logistics network is vital for the businesses that have survived or even prospered in this unsettled climate. Here are five steps for organisations to make their logistics network adaptive and resilient in order to weather any storm and prepare for uncertainty.
1. Build visibility and agility
To adjust quickly to change, you need visibility across your entire supply chain, especially your logistics network. When the first wave hit, companies with a real-time view of their operations knew where to shift volume from one distribution centre to another to avoid challenges. Such speedy adaptation is only possible with a real-time view of the supply chain and logistics operations, including up-to-the-minute inventory accounting.
2. Develop scenario planning capabilities
An intelligent way to equip a business to reply conclusively to rapid market disruptions is by modelling your logistics network. Running what-if scenarios and drafting contingency plans will empower businesses to choose the best course of action in the face of a sudden disruption or emergency.
When the pandemic hit, supply teams of many logistics companies quickly adapted to the outbreak by working closely with other parts of the business to evaluate options. Once aligned on their best estimates – a combination of an optimistic and a pessimistic scenario – companies were able to build supply chain strategies around those scenarios.
3. Setting up automated digital processes
To build an adaptive logistics system, businesses must organise a firmly synchronised series of actions across supply chain functions. This would range from order management and warehousing to last-mile delivery. Cloud-based digital platforms can help secure those connections, connecting systems and exchanging data across the supply chain and with the end customer on one platform.
Many logistics experts have confirmed that next-gen cloud-based logistics solutions were critical to steer their operations successfully through the crisis to allow the digital platform to handle the vast majority of orders.
4. Fortify relationships
Modern logistics networks are complex and interdependent. They comprise thousands or more partners and suppliers participating in these globe-spanning ecosystems. Intricate collaborations promptly across partner networks are vital to absorb any shocks to the overall supply chain. It is always great to have a two-way relationship with your partners. This will suit both parties, showing that each party is invested in the other.
5. Guarantee responsive customer service
At the heart of customer service, there is logistics. Today, consumers and B2B customers expect a smooth and real-time experience from logistics providers. They need accurate ETAs and hyper-responsive customer service. It is said that ‘customer service lives and dies in the supply chain’. In that context, heightening service levels and customer communications during a disruption will ensure massive customer loyalty and repeat business returns.
Digital supply chain technologies and a customer-centric mindset will be critical to achieving delicate responsiveness and accurate order promises. Manufacturing and supply chain visibility will also be essential, allowing you to know and communicate accurately when your customer’s product will be ready to ship.
Leave a Reply